Technical Documentation
Documentation often gets pushed to the side when trying to meet deadlines and get product out the door. We help you meet your customers document requirements so you can focus on production. Meet Occupational Health and Safety requirements, enhance customer knowledge and increase your company’s professional image with professional documentation. Furthermore, while you are working in your business, we can work on the documentation that maps and records your processes, so you can work on your business.
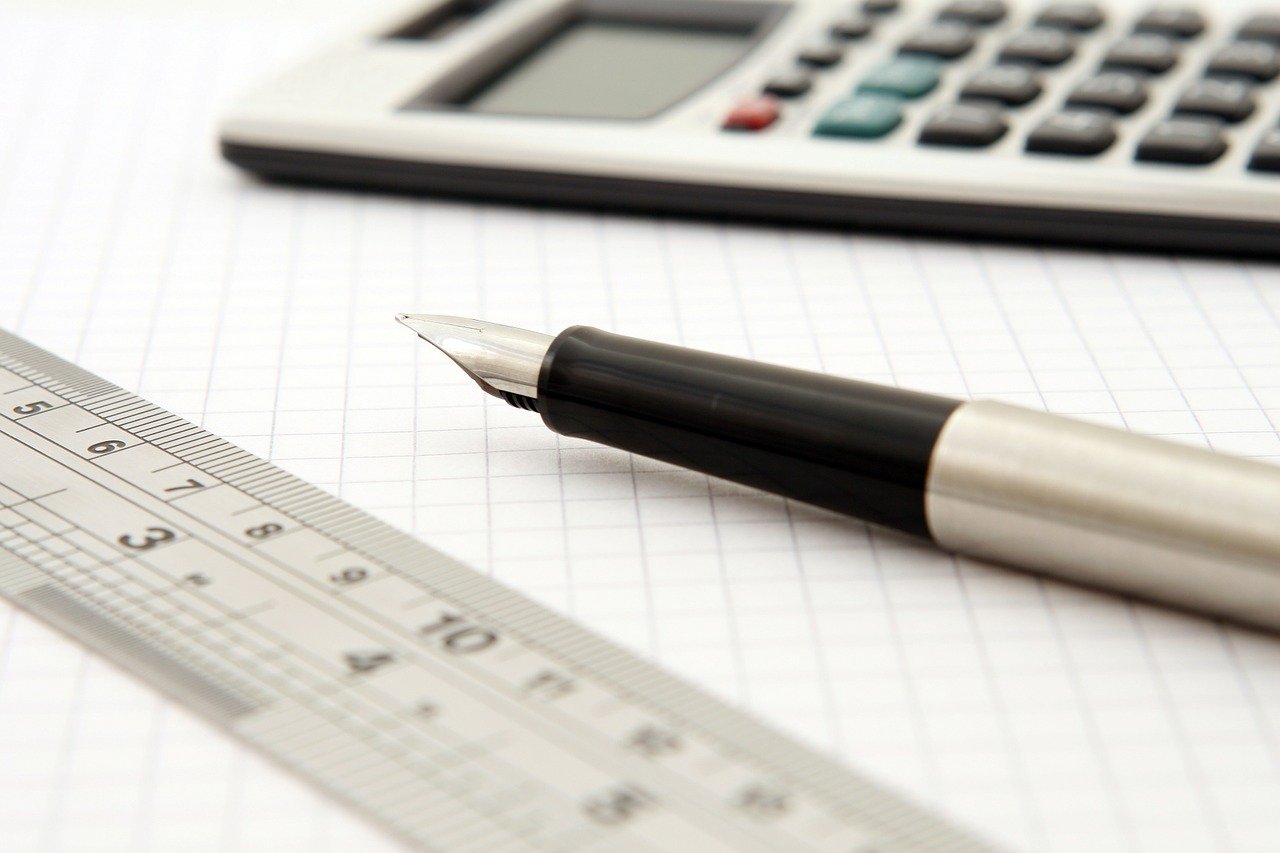
This is a valuable comprehensive document that contains the safety, operating, and scheduled maintenance information that is required to ensure safe and reliable performance of a system and its components. Plants, buildings, and all types of equipment require this documentation to ensure that the people using it can perform their functions safely, correctly, reliably, and repeatedly. OEM approved operating procedures are required to support training that is administered to the people operating, inspecting and maintaining these systems and components.
These detailed diagrams and exploded views are associated part numbers and appropriate descriptions of the components to make it easy for your customers to identify and purchase replacement OEM parts from you or an approved manufacturer. Troubleshooting communication is made easier with accurate illustrations and parts naming conventions.
Visualize your business and operating processes to see information and material flow, how the processes interact with each other and help identify where there are potential improvements to be made.
A critical component of the workflows in a Quality Management System, the SOP contains detailed steps and information to complete a routine task, quality assurance and improve efficiency and performance.
This is a document that provides detailed information on how to perform a specific task of a procedure. It is therefore more detailed than a procedure because it breaks down the task into steps to completion.
Used to communicate product features, specifications and test results in depth so that users can accurately evaluate and integrate the product into their process or system.
Provide your customers with important updates about improvements, repairs, inspections, and/or modifications to the products they have in service.
A service bulletin may also be used to address a question from an end user about a modification or alteration they would like to perform to their equipment and are seeking an OEM approved method. They may be used by OEM’s to provide instructions on how to improve performance, serviceability and safety of the equipment.